The SEM subsystem’s main responsibilities are solar panel design, analysis and implementation, alongside with battery research and selection, and lastly design of the charging circuit.
Photovoltaic (PV) Panel
Selecting the appropriate photovoltaic cell is crucial for Phoenix’s autonomy. The total photovoltaic panel should not only meet the UAV’s energy requirements, but also be suitable in order to be integrated on our aircraft’s wing. For this purpose, the photovoltaic cells ought to have good efficiency but also be flexible to fit the curvature of the wing.
The nominal characteristics of our photovoltaics as well as other important parameters and coefficients, are of high value for the subteam’s members as they provide a complete image of the photovoltaic’s properties and behavior. We use these values to simulate their behavior in various weather conditions using selected software, and some developed by the team.
The SEM subsystem members are responsible for the realization of the photovoltaic panel, which entails designing the specific wiring layout with the appropriate diodes, soldering the individual photovoltaic cells, and aiding in the implementation of the panel on the UAV’s wing.
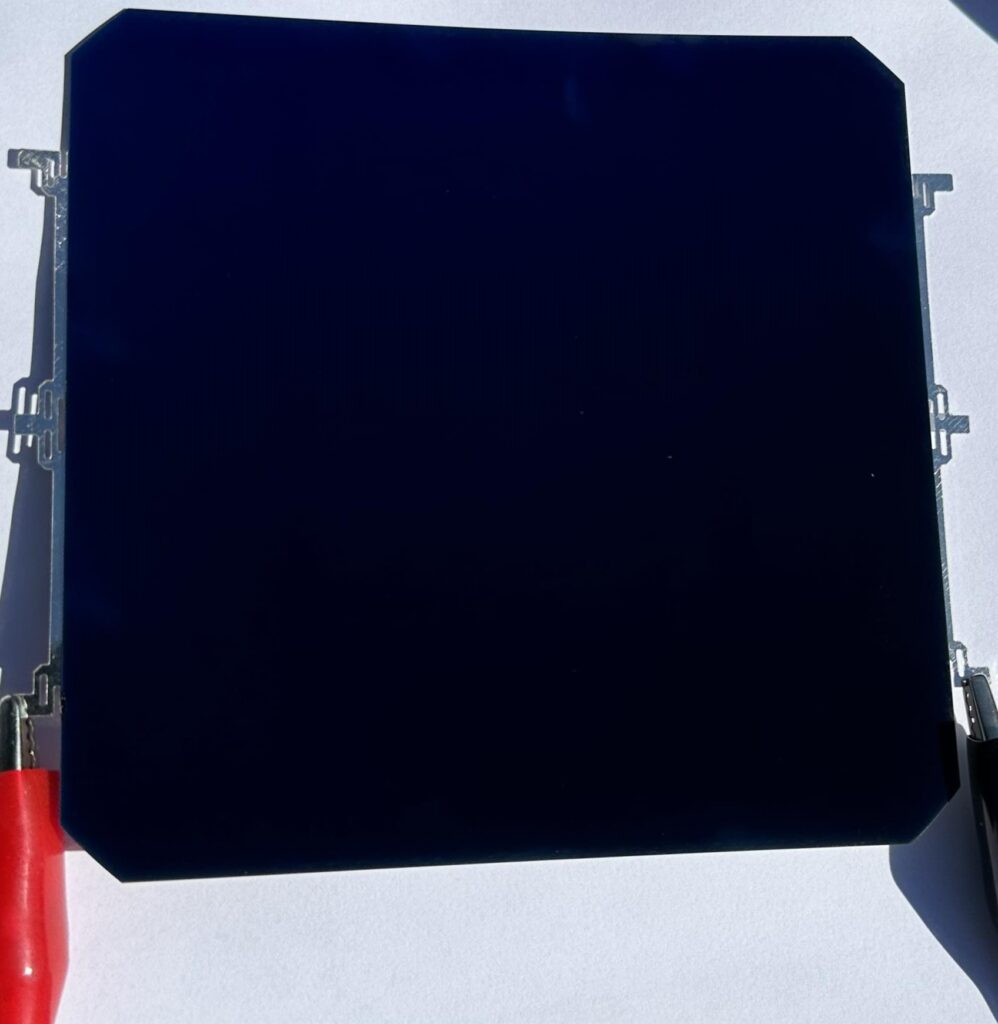
Energy Flow Diagram
The subsystem is also responsible for selecting an appropriate Maximum Power Point Tracker (MPPT) to ensure an efficient and optimal power distribution to the UAV’s propulsion motor, avionics, and Battery Management System (BMS) which leads to the Battery Pack itself.
A picture showing the general configuration is given below.
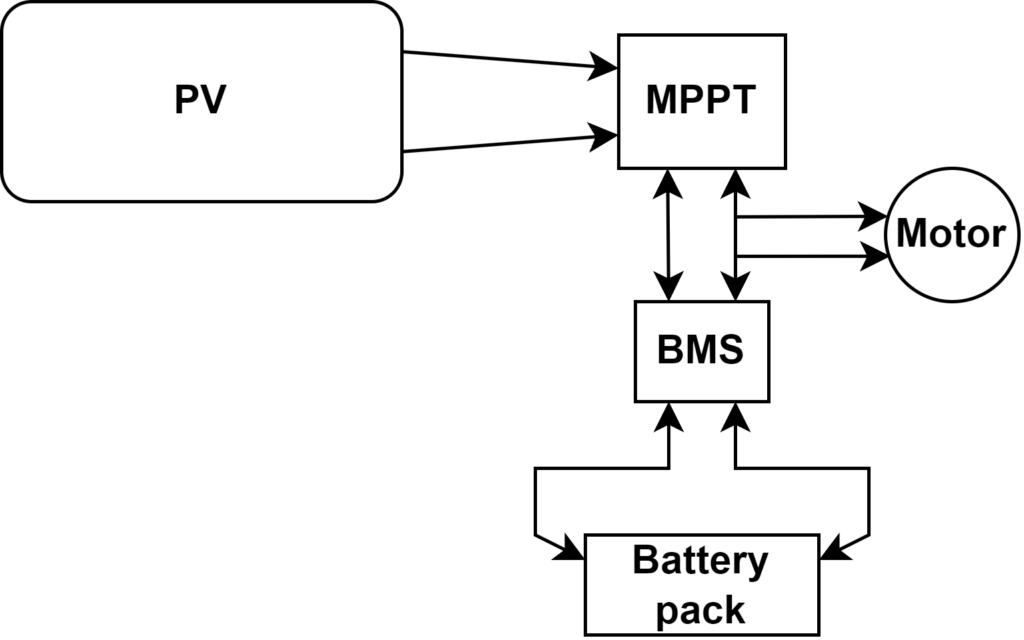
Battery Pack
After the UAV’s energy requirements are set, rechargeable batteries are selected. Li-Ion batteries are preferred for their superior energy density. The Battery pack’s electrical configuration and spatial layout must be carefully thought out and take into consideration the requirements of the electric motor and other peripheral electronics like our MPPT. For safety purposes and to extend the longevity of our battery pack, an appropriate BMS is also selected.
The different charging and discharging characteristics as well as the nominal values of each battery cell are taken into account in the selection process. Afterwards the SEM subsystem conducts thermal simulations in various conditions, thus predicting the charge/discharge cycles inside the UAV’s wing more accurately.