Overview
The Structural sub-system in Aeronautics, is responsible for a part of the aircraft’s design and construction.
In order to better understand its contribution to the project, it is most suitable to see it in action through the design phases and Fabrication processes.
Conceptual Design
In the Conceptual design phase, Structural engineers need to calculate an initial estimation of the UAV’s empty weight, but also the weight ratios between different parts of the aircraft with respect to the overall mass. Their goal is to minimize the empty weight and successively maximize the payload that the UAV can carry.
Furthermore, they are required to bring the center of gravity to the desired location which is defined by the Aerodynamics Design sub-system.

Structural engineers have developed a MatLab code tool, that is capable to predict with a certain level of accuracy, the weight and center of gravity of the UAV. The tool utilizes as inputs the initial dimensions that are given by the aerodynamics design sub-system and returns a weight, alongside a center of gravity estimation with a visualization diagram of the aircraft. This is later confirmed with an initial 3D CAD of the UAV.
As you can see from the first phase of the design, cooperation between the Structural and Aerodynamics Design sub-system is crucial.

During the conceptual design phase, the sub-system is responsible to decide on what materials the UAV will be constructed from. The mission of the aircraft, alongside its weight estimation, needs to be taken into consideration so that the chosen materials can withstand all the stresses and loads that will be induced in flight.
The sub-system performs studies on various materials and selects the most suitable one.
Composite materials, such as Carbon Fiber or Fiberglass, are great options for the aerospace industry because of their advanced properties since they provide the required strength while keeping the weight of the aircraft to a minimum.
Since we mostly utilize composite materials, it is very important to estimate with great accuracy their orthotropic or quasi-isotropic properties. A structural engineer’s goal is to estimate the ABD matrix of a laminated composite and in our case, this is achieved with the classical lamination theory.


Preliminary Design
In the preliminary design phase, one of the Structural sub-system’s responsibilities is to more accurately calculate variables affecting the weight and Center of Gravity of the aircraft.
This is achieved through the generation of a detailed CAD model along with the exact mass calculation of the composite parts of the aircraft through a code-based tool we have developed. During this process, the sub-system also configures all the individual assemblies of the UAV.
More specifically in this design phase, a structural engineer determines the wing box assembly configuration, the tail assembly, performs the process of landing gear sizing, considers wiring routes for the avionics systems, etc.

The most important step for the sub-system in the preliminary design phase is to validate the structural integrity and endurance of the aircraft. This is achieved through finite element analysis due to geometrical complexities and the plethora of structural components.
Finite element analysis is time-consuming due to the extensive tasks that need to be executed in the preprocessing stage, for this reason, structural FEA is performed only on the Wing-fuselage and motor mount assemblies.

The results of every static analysis are being read as stresses in every ply layer of the laminated properties with the failure criteria evaluation method and more specifically the Tsai-Wu reserve factor.
The structural analysis of such structures is a crucial step into the design as it induces changes to our internal components to benefit the weight of the aircraft, determine the ply orientation or strengthen the overall assembly.
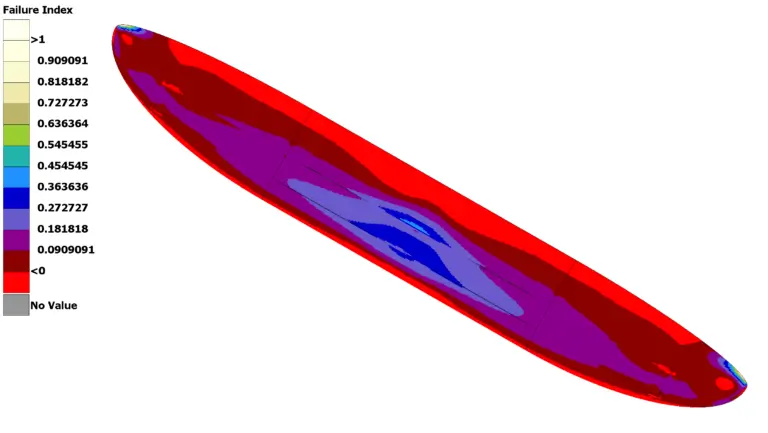
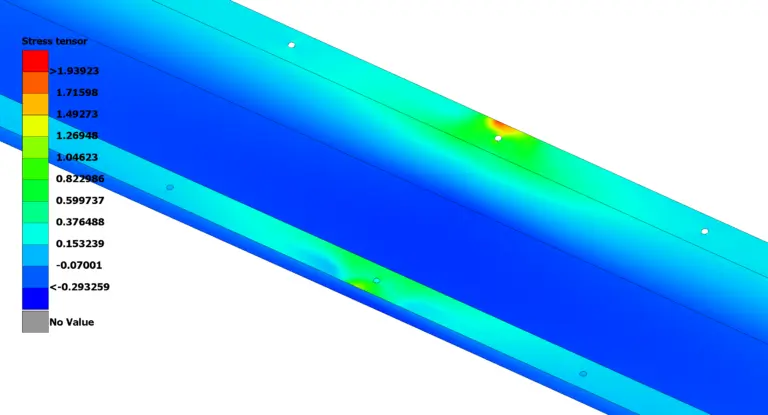
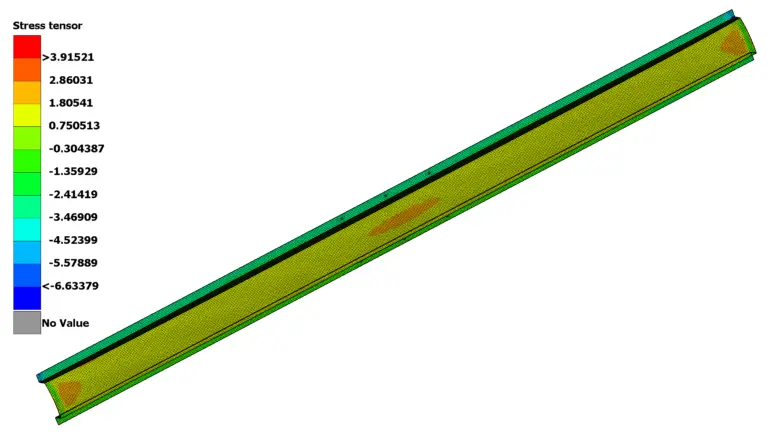
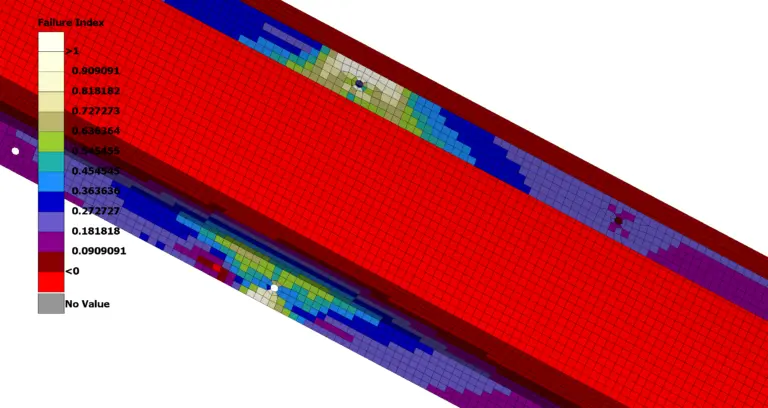
The final step in the preliminary design phase is where every piece comes together and the construction of the UAV is underway. The sub-system is responsible to define the fabrication methods for every part and assembly of the UAV, the parts have to be constructed in the most optimal way to achieve the results estimated by the CFD and Structural FEA analyses conducted previously.
The sub-system utilizes well-known construction methods such as resin infusion, and in certain scenarios, they might need to configure ways by themselves on how the built process will take place.
Construction
The sub-system is also responsible for the construction of the aircraft.
Although all the members of the Aeronautics project contribute to the fabrication of a UAV, the structural engineers delegate the tasks and make sure that the part generation and assemblies are performed correctly and in the right order specified by the fabrication plan.
Moreover, the fabrication plan that contains all the information needed for the construction of a UAV also refers to the safety equipment and the number of people needed in every stage.


Detailed Design & Flights
The final responsibility of the sub-system takes place during flights and it is a part of the detailed design.
While studying the flight performance but also considering the pilot’s feedback on the aircraft’s stability and durability performance, structural engineers along with Aerodynamics Design engineers optimize the dimensions and the structural components of the aircraft where is needed.